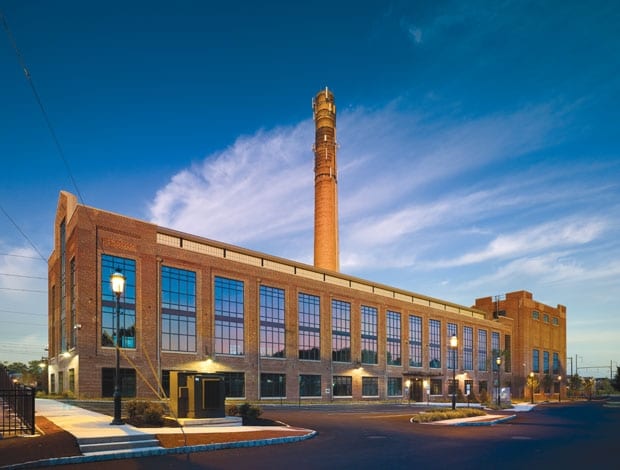
One of the developer’s favourite anecdotes to tell about renovation of the Ambler Boiler House is that when he first saw the project, his son was starting second grade, and now he’s in college. Over those 13 or so years, Heckendorn Shiles Architects (HSA), based in Ambler’s neighbouring town of Wayne, Pennsylvania, has worked on scores, maybe even hundreds, of other projects alongside this one. Now that the labour of love is complete, the cherry on the cake is that the core and shell have been awarded LEED Platinium certification.
Built in 1897, the building was primarily a power station for an asbestos mill, though it had sat vacant for decades before Summit Realty Advisors (the developer, and one of three tenants) and HSA began work adapting it as an office. Despite its derelict state, the exterior – including its trademark roof stack – was relatively well preserved, with just a bit of patching up to do on the brickwork; but inside was a different story. Tonnes of asbestos-contaminated debris had to be removed before an interior restructure changed two storeys to three, and though some of the original steel framing was lost in this process, most columns and roof trusses remained in tact.
“That steel framework really reminds you of the industrial history,” says Matt Heckendorn, HSA’s co-owner, “so being able to preserve those details where we could was very important to us. And obviously that also decreased the amount of material going to landfill or being recycled.” After much research, HSA found a low-emission coating for the steel, used in the marine industry, to prevent rusting.
With preservation high on the sustainability agenda, the interiors focused on exploiting the factory’s character while making sure the development was marketable to tenants looking for a modern work environment. Like the steel structure, the brick masonry is an omnipresent feature, an important echo of the building’s history. Thinking purely from a sustainability point of view, says Heckendorn, these walls would have been covered in insulation, but instead they are a collage of exposed brickwork and new internal walls, maintaining a visual connection with the original structure while hiding services and insulation inside panelling. The tall factory windows were also retained, filled in with highly efficient, low-E glass that allows plenty of daylight without too much heat gain.
“The fundamental goal was a balance between upholding the industrial heritage and providing an interior that serves the needs of contemporary office space,” he sums up. “To a large degree, the design was a series of compromises, from a performance standpoint and for the aesthetics of the building.”
Since splitting up the three tenants floor-by-floor would have seen the employees schlep quite a distance from one end of the building to the other, HSA broke down the vast volume horizontally as well as vertically, giving the three different-sized companies their own bespoke segment. Each company’s office was then designed to fit its working culture. DiD, a healthcare marketing agency, is the largest and the most contemporary, with an open-plan layout, a central ‘communicating’ staircase linking spaces on the second and third floor, and a seashore-themed ‘village green’ with breakout areas and a games room.
On the other hand, the offices for engineering company Core States Group are more traditional, having come from private offices, and Summit Realty’s are somewhere in the middle, with glazed meeting rooms and an open-plan layout, divided by glass partitions. An underlying palette of materials – brickwork, steel, salvaged wood panels (reclaimed from the Coney Island boardwalk) and exposed services – ties them all together. “We were trying to give them each their individual identity, and yet maintain a consistency so that it all felt collectively like part of the Ambler Boiler House,” says Heckendorn.
Construction stalled a number of times due to funding hiccups, finally getting the push it needed from grants and low-interest loans made available – ironically – during the recession. These were largely in support of energy-efficiency improvements: for example, its location on a brownfield site qualified the project for a grant, which paid for a substantial environmental clean-up with minimal landfill and maximal recycling. Its adjacency to a rail station also produced more financial backing in support of public transport, and has done wonders for the local neighbourhood.
Installing a geothermal heat-pump system opened up more funding streams for the project, and massively furthered its sustainability goals, but it wasn’t easy. With a large portion of the site dedicated to storm-water management, HSA had a limited footprint to install the wells within a clear range of the building. This required a specialist geothermal well-field designer, which together with various other experts – including a masonry restoration consultant, plus a large team of mechanical, structural and civil engineers – was invaluable in slotting together the overall composition. “A project like this takes a lot of time and persistence from a really complicated team,” says Heckendorn.
Along the way, the practice has become a bit of a specialist in adapting industrial buildings for office use, having converted an old carriage house into a government office, and an old newspaper-printing house into another workplace. “I think there’s more a common process than a common aesthetic with us. Nothing else quite like this, though,” he laughs. Good job really: at a rate of 13 years a pop, this type of project can only come along once in a while.