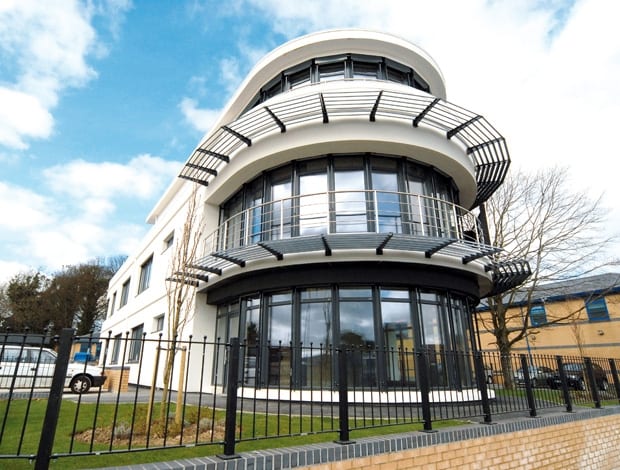
Passivhaus, the utopian benchmark of low-carbon building design is finally finding roots in the UK. Rachel Calton looks at those pioneering the concept
The Passivhaus institute in Darmstadt, Germany, was established almost 15 years ago. However, out of over 15,000 Passivhaus buildings worldwide (nestled mostly in regions of Germany and Austria) you can count the number of accredited UK projects on one hand. A domestic project and training and education centre in Wales share the accolade with one London house, a student residence block at Leeds Metropolitan University, and a row of houses in Scotland.
“We are at a turning point,” explains Gavin Hodgson of the Passivhaus arm of the British Research Establishment Group (BRE), the UK accreditation body. “For the last two or three years there has been a lot of talk of Passivhaus, and competition designs based on it; its an emerging standard that has now made its way into the popular consciousness of architects and designers.”
Hodgson believes its recent take-up is largely down to changes in the overarching political agenda, and drive towards zero-carbon building targets.
Although the two are not directly comparable, Passivhaus is now measured in the same metric as building regulation CO² targets (kWh/m²/yr) and automatically achieves them – by definition a Passivhaus will consume 80-90 percent less energy than an equivalent conventional building, and have a space heating requirement below 15 kWh/m²/yr, but unlike a zero-carbon building, no energy is produced onsite to offset this target.
“The energy saving is in the design and the fabric of the house,” Hodgson explains. “It’s attractive because it cuts the costs and space requirements of putting in onsite renewable energy sources.”
The BRE began disseminating information on Passivhaus five years ago, as part of an EU supported campaign to spread the discipline, which combines excellent insulation, stringent air tightness, well thought out solar gain, minimal thermal bridging and mechanical ventilation heat recovery to create environments that naturally (or passively) control temperature, to a comfortable level in all seasons.
And now, its drive to get a cohort of Passivhaus-trained engineers and architects on the ground in the UK has kicked in. Recruitment for the London-based training, which will begin to run this summer, launched at Ecobuild in March.
“When Passivhaus works, it works well, for life, but it is a technically complicated solution, based on building physics,” Hodgson explains.
The statistical Excel-based Passivhaus Planning Package (PHPP) design compliance tool forms an integral part of the training plan.
“We’re expecting architects and engineers with a background in and understanding of delivering low carbon buildings, to form this crème de la crème of certified Passivhaus designers,” Hodgson explains.
So, with local exemplar projects, UK-based training, and government compatible targets, Passivhaus is certainly taking grip. Embarking on a Passivhaus project in the UK just a few years ago was a very different story. The Beechwood Park office in Dover, coming up for completion this summer, is a project that was initiated four years ago, when one of the partners at property development company WCR Property organised a trip to Freiburg, Germany, the epicentre of Passivhaus, for fellow staff to experience sustainable buildings.
“At the time it was a speculative trip. We already sensed the sustainable market showed very different supply and demand equilibrium than the market for conventional office buildings. It was part of a crystal ball gazing process for us, as to where the market was going to go,” Mike Wallace, property director explains. “We just knew we didn’t want to build any more conventional office buildings.”
It was the sense of health and comfort that the buildings gave, rather than the energy savings, that first sold them on the concept.
“It’s difficult to put into words, “ says Wallace. “But it’s something you can only witness when you step inside a Passivhaus, which is why it’s really important to have projects here in the UK.”
What was planned as a one-off trip to Freiburg, turned into multiple return visits.
“Getting information on sustainable development at the time, and the kind of detailed support and expertise needed to build to the standard in the UK was like stumbling around in the dark,” explains Wallace. “There were a lot of people talking about it, and talk of government policy in support of it, but no practical advice. Eventually we turned to architects in Frieberg, Grießbach and Grießbach, whose experience in Passivhaus projects is numerous. At the time they were retrofitting a local town hall, several hundreds years old, to Passivhaus standard. To apply it to a building that old, made our challenge in the UK seem all the more achievable – with their advice and guidance.
“Passivhaus has now made its way into the popular consciousness of architects and designers”
“Having German and UK architects working alongside each other taught us a lot. It was a case of allowing the expertise to be fed over. In Frieberg, where they have been building to this standard for many years, contractors have got to grips with the concept. No gaps can occur when building to Passivhaus standard, every time you form a seal, it has to be spot on, if it’s not, you do it again – quality control is essential. Here buildings are designed to live and breathe, gaps are built in to the design, so in a way it is a case of re-education. With this level of tenacity, the process can be twice as long, but there are no shortcuts. “Although time predictions can be hard to make when building to Passivhaus, as you are sourcing components from new suppliers in Scandinavia for example, it should improve, as demand grows.” WCR have been working with independent bodies such as the Carbon Trust, monitoring the building’s performance during the process. The first launch of the project took place in March, when the external fabric of the building was complete, and it was four degrees outside. “Everyone turned up with coats and had to peel them off as they got inside. None of the services were connected then so they could be certain the building had never been heated, but by this point the whole place was insulated, airtight, and warm throughout.”
When it comes to letting the building – a speculative three-floor build – communicating the concept of the building will be key.
“Passivhaus is a holistic concept; it can’t be compared to other office spaces on a simple headline rent basis,” explains Wallace.
And it’s not just energy cost savings that give the bigger picture. It’s the air and light quality, which promote health, staff productivity, cut absenteeism and alleviate the symptoms of sick building syndrome.
“Working in one of the most energy-efficient offices in the UK is also a good accolade for a business to have,” says Wallace. “We hope people won’t just see it as 5,000sq ft project in Dover, but will be curious as to the other dimensions of the building.”
Dr Qian Li, partner of architecture firm sustainableBYdesign, agrees that it’s not just the stats and the energy savings that give Passivhaus its USP: “It’s the internal light quality and natural ventilation that is so unique. It offers the occupier a lot more than savings on their bills; it’s an appealing internal environment that we want to offer our clients.”
The practice is currently working on renderings of a Passivhaus school that they hope to see put into construction.
“At the moment, the notion of Passivhaus is just setting in here,” Li explains, “As more schools teach it, the more architecture students become aware of it. It’s a case of spreading this understanding amongst the whole profession; the designer must educate the client, who must educate the developer and so on. At the slower end is the development of regulations to push builders to comply.
“The construction industry has been doing things one way for 20 years. It takes time for change to happen, but the discipline relies on sensible principles, on making the most of natural resources and insulating. Because it is passive, nothing needs replacing, which is a problem when using renewable energy technologies such as photovoltaics. With the rise in energy prices, it’s a discipline that makes a lot of sense. “The technology for Passivhaus is not new, it has been around for 20 years, and only over the last three years it has started to be taken notice of here. Ultimately it’s a route to be followed, it’s a notion. The industry here as a whole needs to be mentally ready and willing to develop it, and to learn from Europe and Germany.”